Steps to follow:
1. | Implement the serial driver accordingly with the tmlcomm.dll interface |
2. | Setup the drive/motor for RS-232 communication |
3. | Set EasyMotion Studio for communication via user implemented serial driver with the drive/motor |
Step 1 Implement the serial driver
| In the main function of the dll initialize the communication channel with the serial settings implemented on the Technosoft drives/motors: 8 data bits, 2 stop bits, no parity, no flow control and one of the following baud rates: 9600 (default after reset), 19200, 38400, 56600 and 115200. |
| Implement the functions for interfacing your communication driver with tmlcomm. This functions are: |
bool __stdcall ReadData(BYTE* pData, DWORD dwBufSize, DWORD* pdwBytesRead)
bool __stdcall WriteData(const BYTE* pData, DWORD dwBufSize, DWORD* pdwBytesWritten)
int __stdcall GetBytesCountInQueue()
void __stdcall PurgeQueues()
DWORD __stdcall GetCommBaudRate()
bool __stdcall SetCommBaudRate(DWORD nNewBaudRate)
where:
pData
|
Pointer to buffer from/to the data is read/wrote
|
dwBufsize
|
Parameter specifying the number of bytes to be read/write from/to serial port
|
pdwBytesRead
|
Pointer to the variable that contains the number of bytes read
|
pdwBytesWritten
|
Pointer to the variable that contains the number of bytes written
|
nNewBaudRate
|
Variable that contains the new value for serial baud rate
|
| Export the functions from the communication driver using a module-definition (.DEF) file with the following content: |
LIBRARY "virtRS232"
DESCRIPTION 'Example of a virtual serial driver for tmlcomm.dll'
EXPORTS
; Explicit exports can go here
ReadData
WriteData
GetBytesCountInQueue
PurgeQueues
GetCommBaudRate
SetCommBaudRate
Step 2 Setup the drive/motor for RS-232 communication
1. | Power-Off your drive/motor |
2. | In order to use the RS-232 communication, you need to connect your PC with the Technosoft drive/motor through an RS-232 serial cable. If the drive/motor is equipped with a standard 9-pin DB9 connector for serial communication, use a 9-wire standard serial cable: male-female, non-inverting (e.g. one-to-one), else check the drive/motor user manual for cable connections. |
3. | If the drive/motor supports also RS-485 communication, set the RS-232/RS-485 switch (or solder-joint) to the position RS-232. |
4. | Power-On the drive/motor |
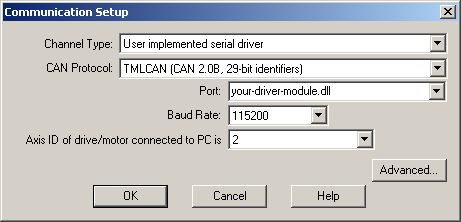
Step 3 Set EasyMotion Studio for communication via user implemented serial driver with the drive/motor
1. | Select menu command “Communication | Setup” |
2. | Select User implemented serial driver at “Channel Type”. |
3. | Select the “CAN Protocol” between the drives/motors connected in the CAN-bus network, the drive/motor connected to PC acting as a retransmission relay (see Communication Protocols). You can choose either TMLCAN (CAN2.0B, 29-bit identifier) or CANopen or TechnoCAN (CAN2.0A, 11bit identifier). |
4. | Specify at “Port” the communication dll you implemented |
5. | Select the desired baud rate from “Baud Rate” list |
6. | Set the “Axis ID of the drive/motor connected to PC”. The default option is autodetected enabling EasyMotion Studio to detect automatically the axis ID of the drive connected to the serial port. If your drive/motor doesn’t support this feature (see remark below) select its axis ID from the list. The drives/motors axis ID is set at power on using the following algorithm: |
a. | With the value read from the EEPROM setup table containing all the setup data |
b. | If the setup table is invalid, with the last axis ID value read from a valid setup table |
c. | If there is no axis ID set by a valid setup table, with the value read from the hardware switches/jumpers for axis ID setting |
d. | If the drive/motor has no hardware switches/jumpers for axis ID setting, with the default axis ID value which is 255. |
Remark: When the TechnoCAN communication protocol is used the Axis IDs, of the drives/motors and of the PC, are interpreted as modulo 32.
If the communication works properly, you’ll see displayed on the status bar (the bottom line) of the EasyMotion Studio the text “Online”, the axis ID of the drive/motor and the firmware version read from the drive/motor.
Remark: If your drive/motor firmware number:
• | Starts with 1 – examples: F100A, F125C, F150G, etc., or |
• | Starts with 0 or 9 and has a revision letter below H – examples: F000F, F005D, F900C |
you can’t use the axis ID autodetected option.
See also:
User Implemented Serial Driver Example
User Implemented Serial DriverTroubleshoots
Advanced Communication Setup
Communication Setup
|