Technology
Technosoft has pioneered the intelligent drive as a cost-effective solution in many motion control applications. Embedding a motion controller and a drive into a single unit, an intelligent drive can perform many of the tasks that are traditionally assigned to a central unit. Using TML — a high-level programming language, Technosoft intelligent drives can independently execute complex motion programs that involve:
- setting of all supported modes of operation
- control of advanced program flow, such as conditional jumps, function calls, interrupts, wait loops, special events
- execution of numerous standard and user-customized homing modes
- handling of all I/Os
- arithmetic and logic operations
- use of one intelligent drive as an “application master”, which controls the other drives
- data transfers among axes
- synchronization with all other axes’ control loops
The next step was the intelligent motor, which integrates an intelligent drive within a motor. Thus, motion controller, drive and motor are all grouped into a single compact unit, which receives motion commands via a communication channel and translates them into mechanical movements.
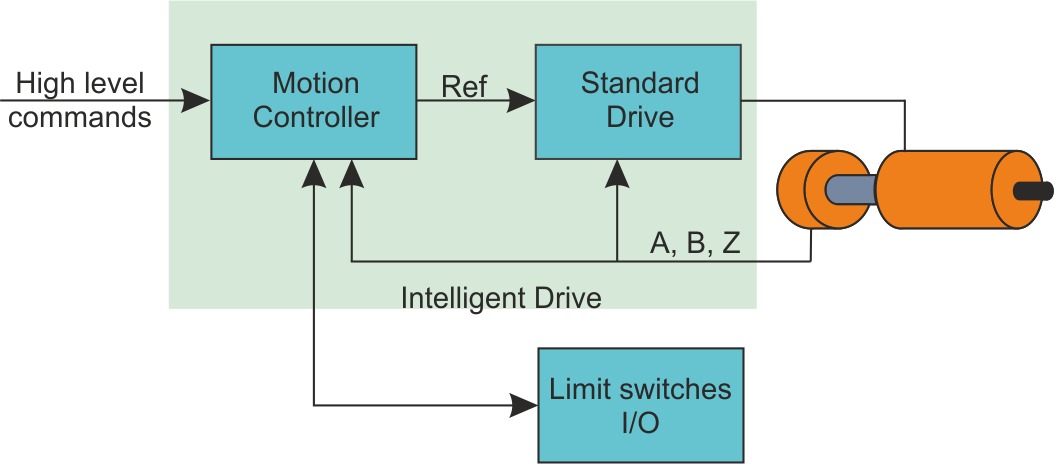
Schematic of an intelligent drive
Schematic of an intelligent drive
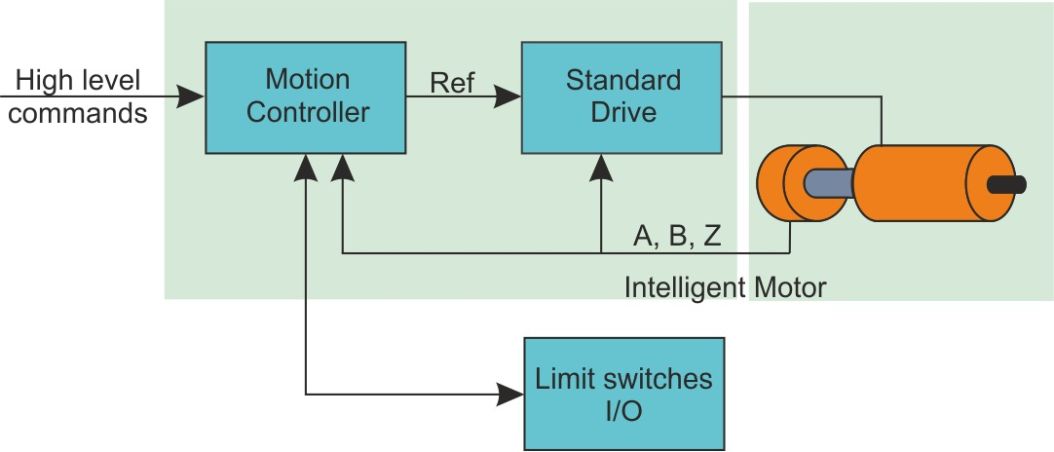
Schematic of an intelligent motor
Schematic of an intelligent motor
The MotionChip™ Concept
MotionChip™ is an advanced Technosoft concept realized as a high-performance ready-to-run motion controller based on dedicated processors. Using up to 8 PWM signals, this chip can drive either one or two H-bridges, or a 3-phase inverter, providing a single-chip solution to the control of rotary or linear brushless, DC brush and 2-phase or 3-phase step motors. Operation modes include torque, speed and position control with various options like: Hall-sensors based DC mode, or vector-control based sinusoidal AC mode for brushless motors control; open loop with micro stepping, or closed-loop (vector) control of steppers. MotionChip™ has a built-in motion controller with a high-level language for motion programming: TML (Technosoft Motion Language). Thanks to the powerful TML instruction set, complex motion applications can programmed directly at drive level, eliminating in many cases the need for a separate motion controller.
Features
- All in one solution: controls linear or rotary brushless, DC brush and step motors
- Easy application programming via TML – a high level motion language
- Various modes of operation: open loop, torque, speed and position control
- Standalone or master/slave operation, with complex motion sequences
- Single- or multiple-axis configuration
- Multiple feedback options: incremental quad and sine-cosine encoders, digital and linear Halls, tacho-generators, absolute encoders and resolvers
- Multiple communication channels: RS-232, CAN, Ethernet, EtherCAT
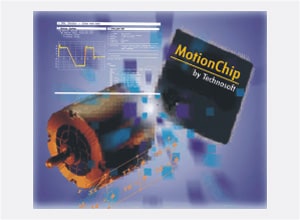
Benefits of Technosoft Motion Technology
asdas
- All in one: controller and drive in a single unit
- One for all: same drive for DC, stepper, brushless and linear motors
- Distributed intelligence with complex motion programs executed by the drives
- Advanced motion control (dual loop, PVT, S-curves, electronic camming) with the TML programming language
- Multiple communication options: RS232, TMLCAN, CANopen, EtherCAT, Ethernet
- Easy implementation with motion control function libraries for PC (C/C++, Visual Basic, Delphi, LabVIEW, Linux) and PLC (Simatic S7, Omron CJ1, B&R X20)
- Graphical programming with EasyMotion Studio
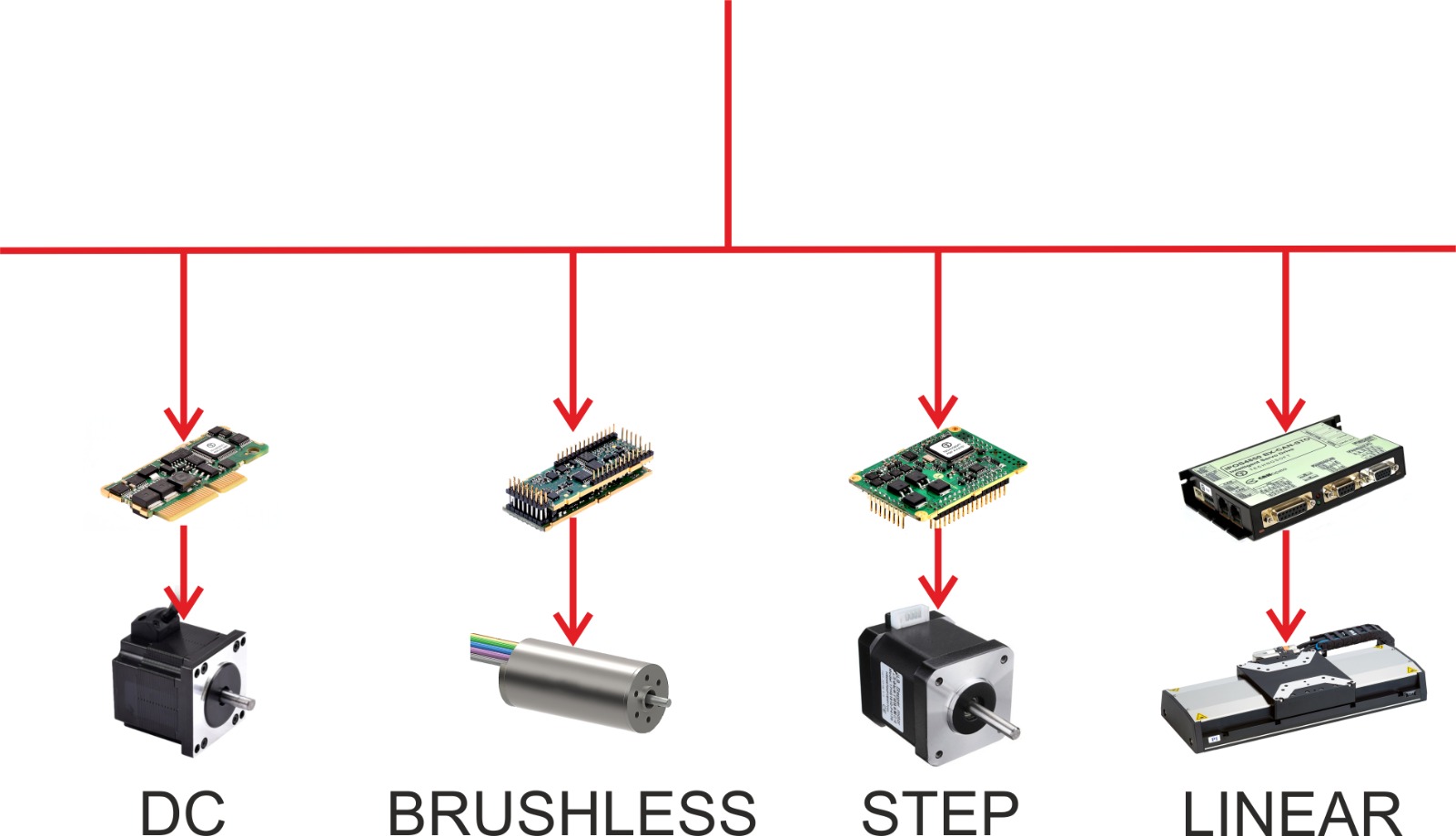
TMLCAN. CANopen. EtherCAT
Technosoft products with CAN interface can operate in 2 modes: TMLCAN and CANopen.
When the TMLCAN mode is selected, Technosoft drives and motors act as intelligent drives & motors and conform to the Technosoft protocol for exchanging TML commands via CAN-bus. When the TMLCAN protocol is used, it is not mandatory to have a master. Any drive can be set to operate stand-alone and may play the role of a master to coordinate both network communications/synchronization and the motion application through TML commands sent directly to the other drives.
When the CANopen mode is selected, Technosoft drives and motors behave as standard CANopen devices that conform to CIA 301, 305, and 402 profiles. In this mode, a CANopen master is needed for application control. The drives/motors can still perform complex motion functions, written in TML and stored in their EEPROM memory, with the CANopen master having the option to call these functions. Using this decentralized approach, where the CANopen master calls functions to be executed and then waits for their completion confirmation, the overall computation and the communications needs can be substantially reduced, leading to better, more cost-effective solutions
On most products of the new iPOS and iMOT lines, both TMLCAN and CANopen options are present. Through a hardware switch, either one or the other is activated after power-on.
Technosoft products with an EtherCAT interface operate as standard EtherCAT devices that conform to the CAN application protocol over EtherCAT (CoE). As with CANopen versions, Technosoft drives/motors can still perform complex motion functions, written in TML and stored in their EEPROM memory, so that the EtherCAT master has the option of calling these functions.
TML: Technosoft’s Motion Programming Language
One of the key advantages of Technosoft intelligent drives and motors is their ability to execute complex motions without requiring an external motion controller. This is possible because Technosoft drives offer, in a single compact package, both a state-of-the-art digital drive and a powerful motion controller. This gives you the following options of implementing a motion application:
- As a standalone motion program, written in TML and stored into the drive’s non-volatile memory, which is executed automatically after power-on;
- In a central unit, where the motion application is implemented using one of the TML_LIB motion libraries for PC or PLC. In this case, the TML commands are sent one by one through a communications channel;
- Using a decentralized control approach which combines the above options, like for example a host calling motion functions programmed in the intelligent drives/motors using TML.
TML (Technosoft Motion Language) is a high-level language that lets you program complex motion profiles for the intelligent drive/motor to execute independently. TML allows you to:
- Set various operation modes: position or speed profiles, PVT or PT interpolation, electronic gearing or camming, external reference, etc.
- Change motion modes and/or motion parameters on the fly
- Execute standard homing modes, or your own customized versions
- Control the program flow through:
-
- Conditional jumps and function calls
- Interrupts generated on pre-defined or programmable conditions (protections triggered, transitions on limit switch or capture inputs, etc.)
- Waits for programmed events to occur
- Handle digital I/Os and analogue input signals
- Execute arithmetic and logic operations
- Perform data transfers between axes
- Control the motion of an axis from another axis, via motion commands sent between axes
- Send commands to a group of axes (multicast). This includes the possibility of simultaneously starting motion sequences on all axes in a group
- Synchronize all the axes in a network
With TML, you can really distribute the intelligence between a master and the intelligent drives/motors in complex multi-axis applications. Thus, instead of trying to command each step of an axis movement, you can program the intelligent drives/motors, using TML, to execute complex tasks and inform the master when these tasks are done. Thus, for each axis, the master’s task may be reduced to calling TML functions and waiting for a message that confirms the end of their execution. If needed, the intelligent drives/motors may also be programmed to periodically send information messages to the master, so it can monitor a task’s progress.
Due to a powerful instruction set, the motion programming in TML is quick and easy, even for complex motion applications. The result is a high-level motor-independent program which — once conceived — may be used in other applications, too.
The TML motion programming can be easily done using EasyMotion Studio. This includes a Motion Wizard which allows you to program your application in a simple, graphical way, through a set of programming dialogues. When a programming dialogue has been closed, the associated TML instructions are automatically generated.